Datwyler opens first US production plant, boosting output by 50%
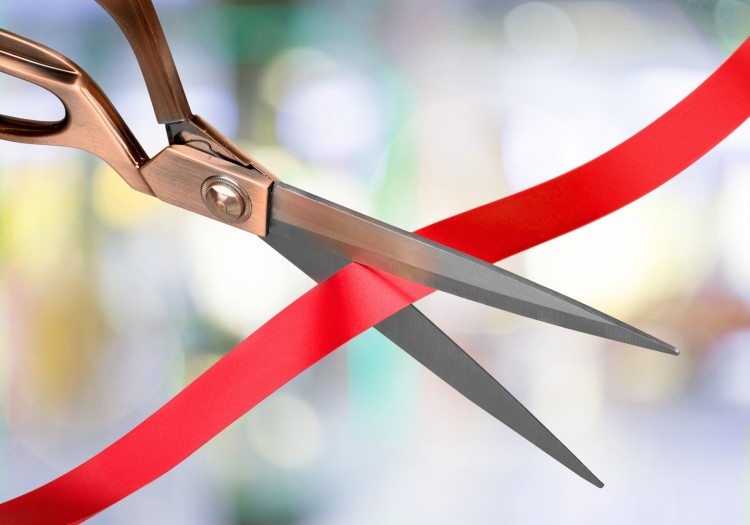
The facility will be the Switzerland-headquartered company’s third facility, joining First Line plants in Alken, Belgium and Pune, India.
Omni Flex components will be manufactured at the plant, which are used in pharmaceutical containers and pre-filled syringes for biological products.
Further explaining what the technology involves, David Clark, vice president of operations for the Americas, told us Omni Flex provides “a lubricous barrier coating that does not require siliconisation prevents interaction with leachables and extractables that could render the drug dangerous or ineffective.
“Omni Flex coated plungers are manufactured using a proprietary, flexible, fluoropolymer spray coating technology. The technology is designed to (1) be an inert barrier and (2) impart a low coefficient of friction for non-siliconized pre-filled syringe plungers,” he added.
The facility cost more than $100m (€87.35m) to construct and will create approximately 120 jobs in the Middletown, Delaware area. With this newest facility opening, the company states that it will be able to increase global First Line production 50% by 2020.
Discussing the location, Clark told us that the Middletown area is situated in a “pharmaceutical hotbed” where many of the company’s customers are located. In addition, he said that the foothold in the US will allow the company to access the largest market for rubber components in the industry and is of “strategic importance”.
In terms of what First Line production facilities offer, Clark detailed how: “The manufacturing concept is based on ultra-modern cleanroom technology, automated production cells, fully automated camera inspection, and a unique validated washing process. Furthermore, a zoning concept is implemented. Each zone has been meticulously designed and constructed in order to prevent bio-contamination and is equipped with material and personnel airlocks.”
He went on to detail that the plant is operated under a “zero-defect policy”, and offers the lowest endotoxin, bioburden, particulate, and defect levels available in the industry.